GRI 102-7, 201-1, 416-1, 417-1
solutions
Our flexibility enables us to participate in strategic areas of the automotive industry.
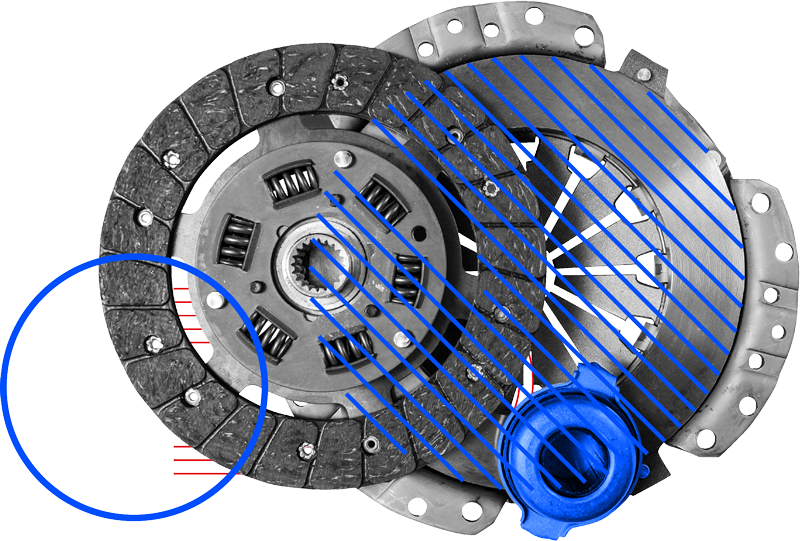
Our flexibility enables us to participate in strategic areas of the automotive industry.
Develop structural and safety components that surpass all engineering performance requirements leveraging on advanced material, lean and flexible processes, achieving successful program launches.
We are a full-service partner to major automotive Original Equipment Manufacturers (OEM) and provide additional services:
We provide products and solutions for multiple customers worldwide in several brands and markets, from basic utility vehicles through high luxury vehicles.
Our commitment to quality, service and innovation has been recognized and rewarded by our customers and the communities where we operate. Some of the awards we received this year are:
We strive to deliver the best products with exceptional quality. Hence, through our customer scorecards, we receive feedback regarding our overall performance; customers evaluate the products’ quality, delivery, cost, warranty, among others, so we can improve any glitches.
Our main safety assessments are related to our products’ welding and geometry. We carry out special procedures and verification processes that are intended to ensure the integrity of the welding. These take into account Metalsa’s best practices, lessons learned, and documented processes created by our Joining System Knowledge Center and AIAG Welding System Assessment (CQI-15) standard.
All our designs are submitted to virtual simulations of the forming process and vehicle durability to find any thinning or fracture of the material, as well as any fatigue that degrades the performance of the components Metalsa supplies. Some physical tests are performed for prototypes, including four posts, track durability, rolling and towing dynamometer, among others, so the results obtained from simulation are verified.
Chemical substances contents and material compositions in our products are verified through the Material Data Sheet and some other customer assessments, which are uploaded into the International Material Data System (IMDS) or any other platform indicated by our customers as part of our Production Part Approval Process (PPAP) and that of our own suppliers, so we verify that we comply with all regulations related to end-of-life vehicle directives and those unique for each one of our customers
During 2020, we had no non-compliances or grievances regarding negative health and safety impacts or related to our products’ information.